Discover Reliable Packaging Equipment Repair Services for Your Business Needs
Discover Reliable Packaging Equipment Repair Services for Your Business Needs
Blog Article
Specialist Solutions for Streamlined Packaging Tools Maintenance and Fixing Services
Professional services that utilize anticipating maintenance methods and utilize IoT modern technology supply a pathway to decrease unforeseen downtime and reduce costs. As organizations seek to boost their operational efficiency, one must consider how these cutting-edge strategies can change maintenance practices.
Anticipating Upkeep Techniques
In the world of product packaging tools upkeep, anticipating upkeep methods have actually arised as a transformative strategy to decreasing downtime and enhancing operational performance. Predictive maintenance depends on condition-monitoring tools and IoT-enabled sensing units that constantly examine the operational state of equipment.
It allows organizations to transition from responsive to aggressive upkeep approaches, decreasing the frequency and extent of devices failures. Predictive upkeep contributes to set you back financial savings by lowering the need for emergency situation repair work and lessening manufacturing interruptions.
Purposefully, firms that embrace anticipating maintenance gain an affordable side by boosting equipment integrity and overall performance. As innovation proceeds to develop, the integration of anticipating upkeep methods into packaging equipment upkeep programs will significantly end up being a typical practice, driving sustainable functional renovations.
Reliable Fixing Protocols
Simplifying the repair service process is critical for keeping the functional performance of product packaging tools. These guidelines must be conveniently easily accessible to maintenance workers and regularly upgraded to incorporate the most current technological developments and market standards.
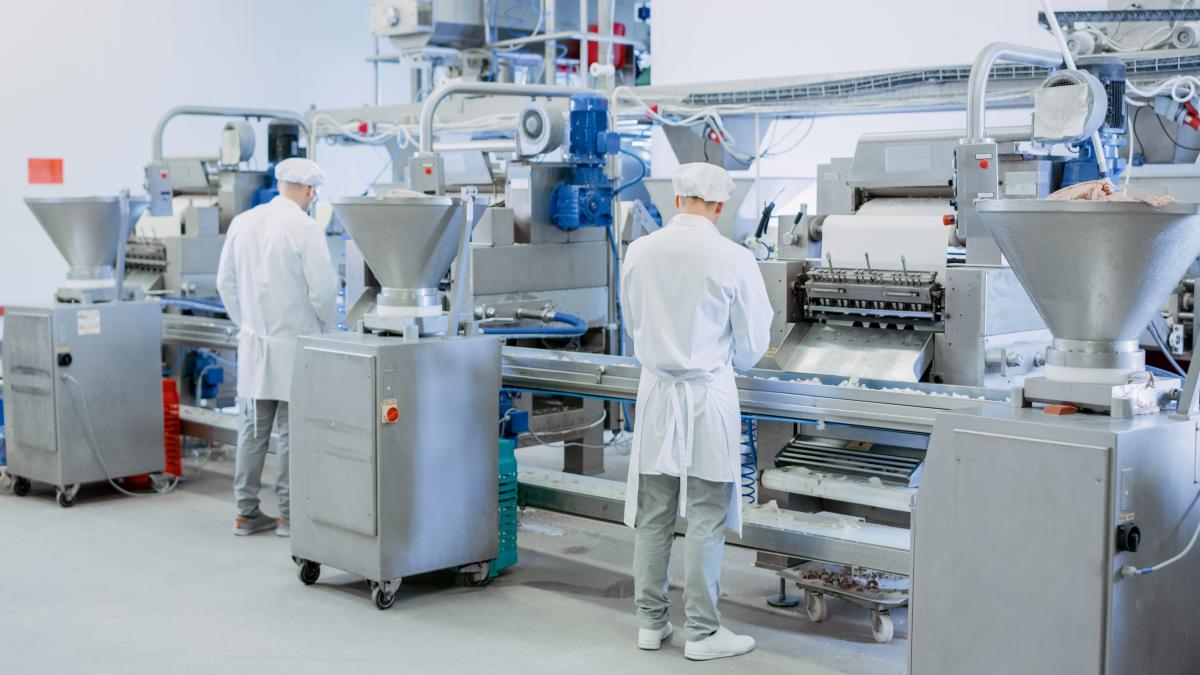
Training maintenance teams in these procedures is similarly important. Normal workshops and hands-on training sessions equip employees to execute fixings quickly and precisely. Cultivating a society of constant enhancement motivates feedback from professionals, leading to improvements in repair approaches and procedures.
Advanced Diagnostic Devices
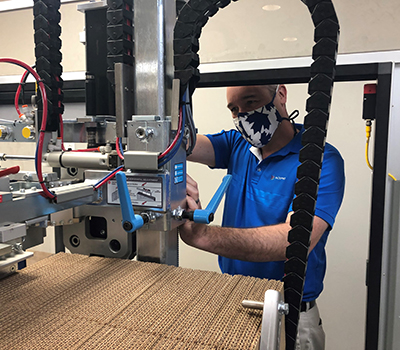
Advanced diagnostic devices offer thorough understandings right into the problem of packaging machinery. Thermal imaging video cameras can discover overheating parts, allowing for prompt intervention. Resonance analyzers monitor equipment resonances, recognizing variances that may indicate mechanical mistakes, while ultrasonic detectors can pinpoint air leakages or electric discharges that are not noticeable to the naked eye. These devices jointly add to a more educated and accurate maintenance strategy.
Additionally, incorporating innovative analysis devices into upkeep methods makes it possible for data-driven decision-making. The accumulated data aids in anticipating devices failings and preparing targeted repairs. Services can allot resources more properly, decrease maintenance prices, and boost the total integrity of their product packaging systems.
Training and Ability Development
The performance of innovative analysis tools is significantly improved when paired with thorough training and ability advancement for maintenance employees. Training programs customized to the details requirements of packaging tools are essential.
Skill development campaigns can take numerous forms, including workshops, accreditation programs, on-the-job training, and cross-training amongst employee. Stressing continuous discovering makes certain that technicians are abreast of the most up to date technological improvements and maintenance techniques. Furthermore, spending in skill development promotes a society of technology and problem-solving, allowing upkeep groups to resolve tools problems proactively.
In addition, well-trained employees add to lessening downtime and maximizing equipment performance, inevitably resulting in boosted functional efficiency and price financial savings. Creating an organized training strategy, lined up with business objectives, guarantees that the labor force is experienced and confident in maintaining read here high criteria of devices treatment. This critical approach to training and ability advancement is critical in attaining structured maintenance procedures in the packaging market.
Leveraging IoT and Automation
In today's rapidly progressing packaging iot, market and automation are changing maintenance methods, providing unprecedented degrees of effectiveness and accuracy. By integrating IoT-enabled sensing units and devices, product packaging tools can currently communicate real-time information concerning functional condition and possible faults. This connection permits for anticipating upkeep, where issues are recognized and resolved prior to they rise into costly failures, thus lessening downtime and expanding equipment life expectancy.
Automation more enhances these abilities by automating routine maintenance tasks and diagnostics. With the execution of automated systems, companies can enhance their maintenance schedules, decreasing hand-operated intervention and the margin for human mistake. Automated reports and signals generated by IoT devices make certain maintenance groups are always educated, promoting a positive technique to tools care.
Moreover, the combination of IoT and automation promotes smooth information analysis, making it possible for better decision-making processes. By using data analytics, organizations can get insights into devices efficiency patterns, maximize resource appropriation, and improve general functional effectiveness. This technological harmony not just minimizes maintenance expenses but also boosts performance and dependability in product packaging procedures. As the sector proceeds to advance, leveraging IoT and automation is critical for keeping an one-upmanship in tools maintenance.
Conclusion
The assimilation of anticipating maintenance methods, reliable repair procedures, and advanced diagnostic devices substantially boosts product packaging equipment repair and maintenance services. By leveraging IoT and automation, prospective failures can be prepared for and attended to proactively, therefore lowering downtime and prices. Structured training and ability development for service technicians even more make certain the speedy implementation of required repair services. This thorough approach not just extends the life expectancy of tools yet also enhances productivity and integrity, ultimately enhancing operational efficiency in product packaging operations.
In the world of packaging devices upkeep, predictive upkeep methods have actually emerged as a transformative technique to lessening downtime and enhancing functional performance.Utilizing sophisticated analysis tools is pivotal in enhancing the upkeep and fixing of product packaging tools. In addition, investing in skill development fosters a culture try here of technology and analytic, enabling upkeep groups to address equipment problems proactively.
Automated signals look at this now and reports produced by IoT tools make sure maintenance teams are constantly educated, advertising a proactive method to tools care.
The integration of anticipating maintenance methods, efficient repair methods, and progressed diagnostic devices significantly enhances product packaging devices upkeep and repair service solutions.
Report this page